Sheet metal cutting is the initial phase of the production process. This operation can be performed using laser or plasma cutting machines, to obtain a precise and clean cut. The machines can also mark the parts with a casting number or any other text/number as may be needed by the customer.
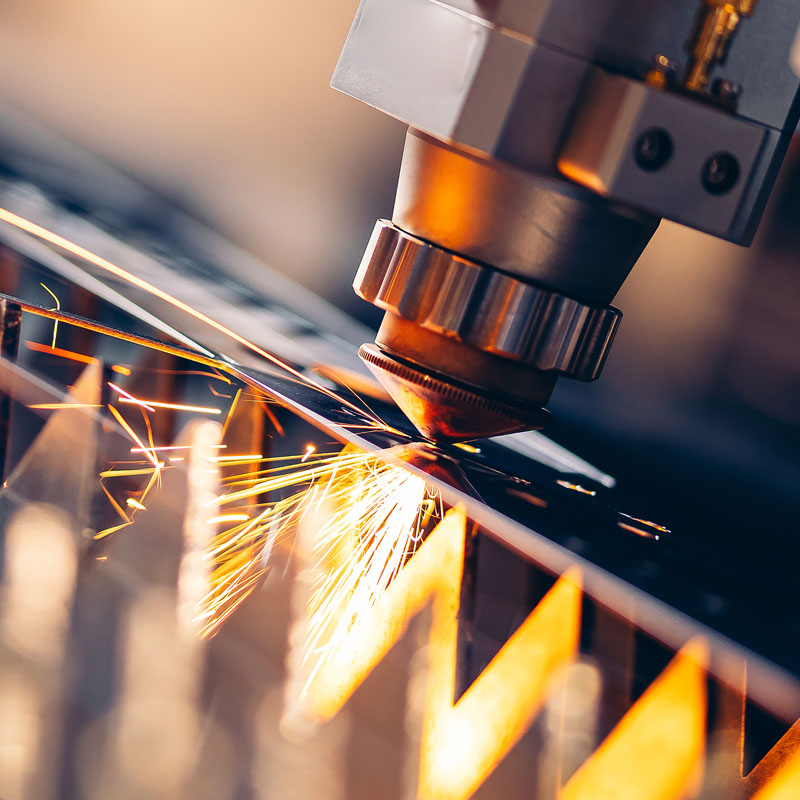
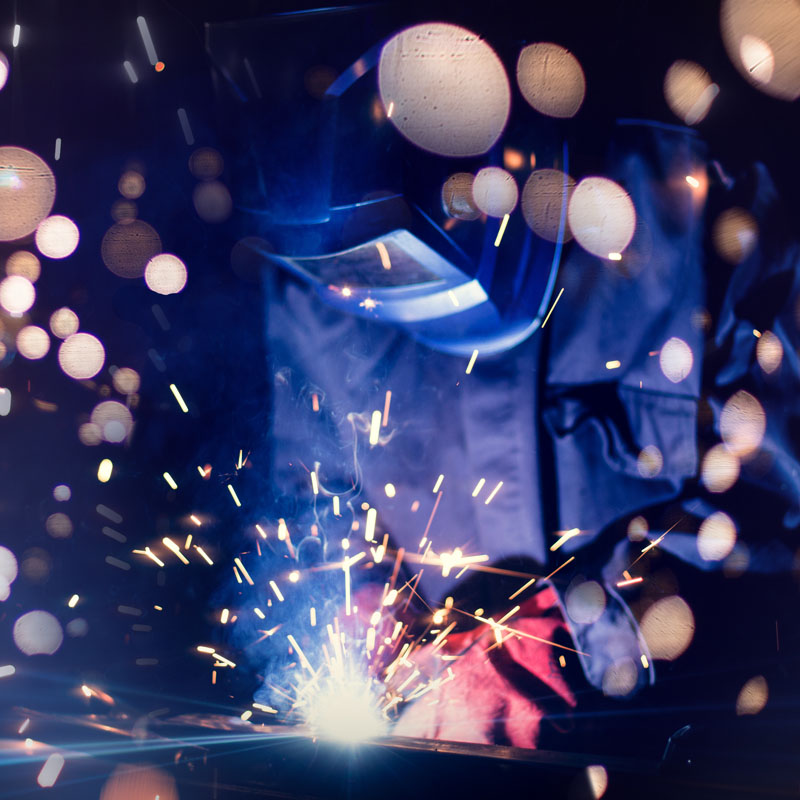
Welding
When it comes to producing top quality stainless steel products, welding is a critical phase of the production process. To ensure maximum efficiency and safety, we use different welding techniques, including plasma, submerged arc, TIG or MIG welding. The welding process quality is guaranteed by acknowledged procedures and up-to-date process and operator qualifications, such as WPS/PQR/WPQ according to ASME and EN for PAW (plasma), SAW (submerged arc) GTAW ((TIG) and GMAW (wire) automatic/manual methods.
Crowning
Crowning with a hydraulic press is a machining technique that requires precision and skills from the operator. The press is equipped with a specific die which allows the required crown radius to be obtained; during the process the press carries out several pressing cycles which gradually deform the disc until the desired spherical shape is obtained. The operator, using special templates, constantly verifies the correct implementation of the required crown radius. At the end of the process, a final check is carried out to guarantee conformity of the product with the requirements.
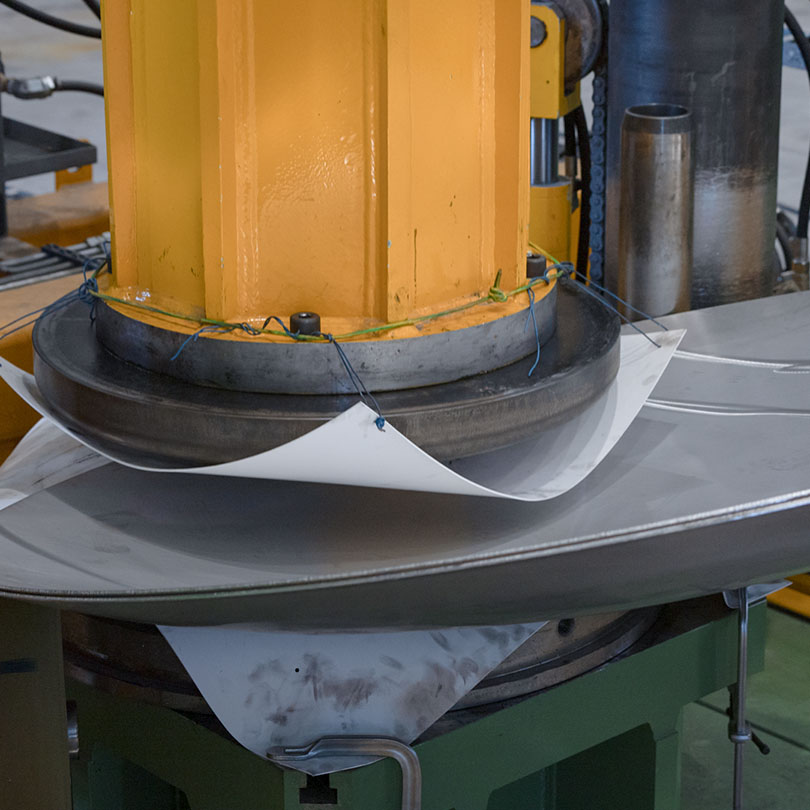
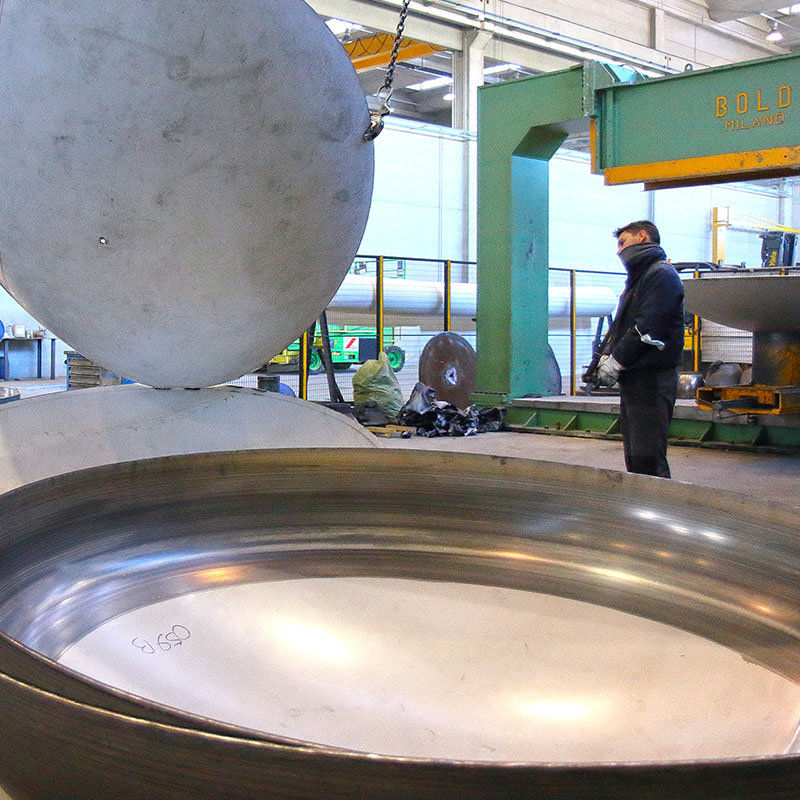
Forming
In this type of production process, the deformation is generated by heavy pressure applied simultaneously over the whole surface of the disc. The initial disc, locked between the die and the blank holder, is machined into the desired shape by large volumes of air or water conveyed from the main tank to the disc, deforming the plate to the depth value set by the operator, who at the end of the process ensures compliance with the required radius with the help of special templates. These technologies allow products with complex shapes to be created, guaranteeing highs level of precision and quality.
Knuckling and Bevelling
Knuckling gives the final profile to the head starting from a dished only head. Thanks to the use of interchangeable shaper rollers, we can meet the expectations of our customers in terms of their required “r” radius. Chamfering prepares the edge of the head according to a design or description submitted by the customer, using a plasma cutting machine. After processing, both a visual inspection and a measurement of the height and circumference of each head are carried out.
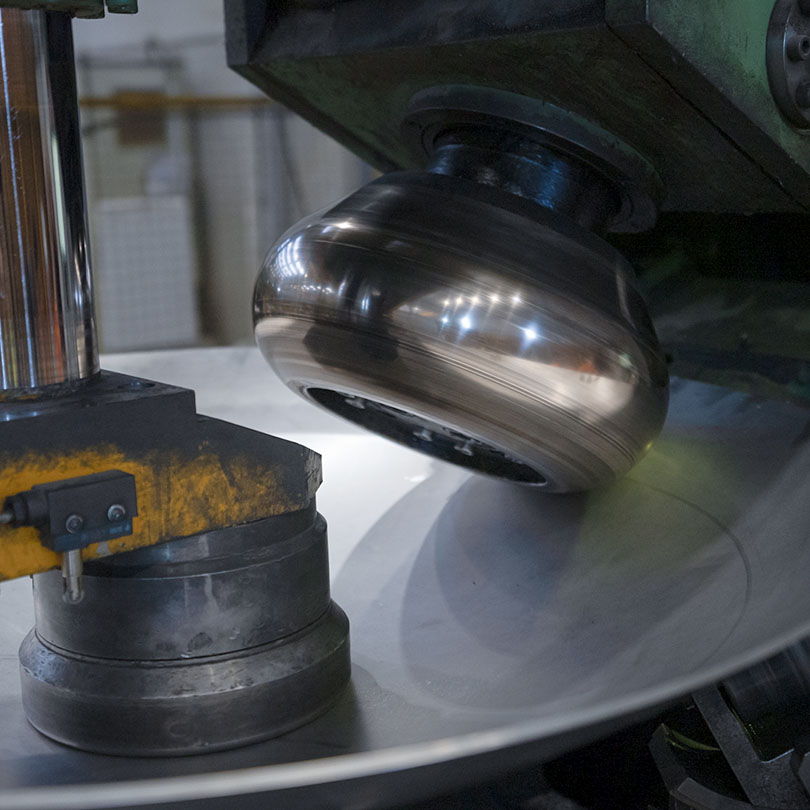
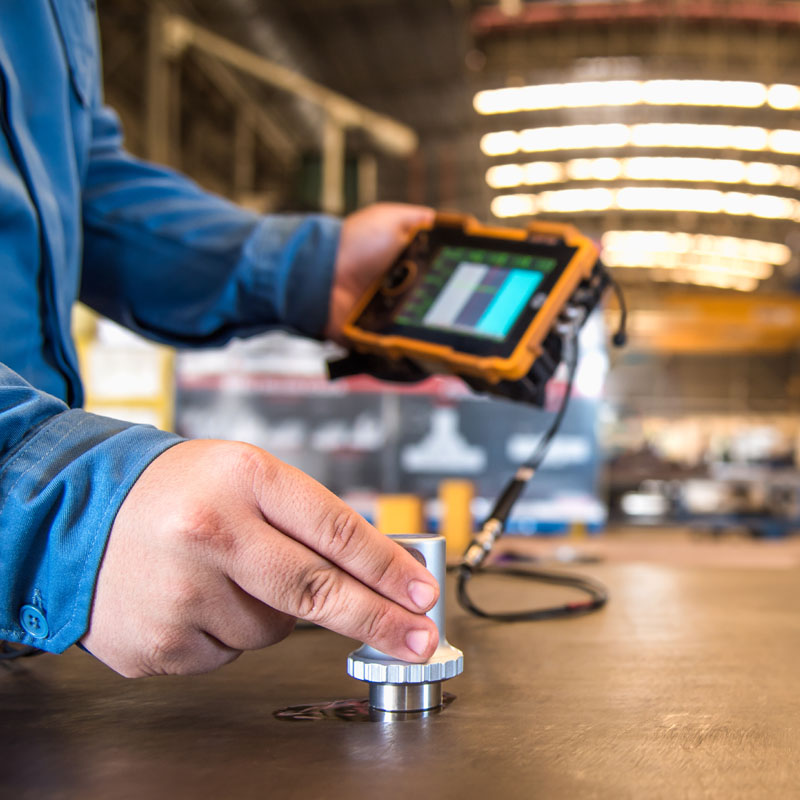
Radiographs and Tests
During the processing phase, ensuring end product quality is essential. In addition to the checks carried out during each operation, in the event that a minimum guaranteed thickness is required after forming, thickness decrease is monitored using a digital ultrasound thickness gauge. Upon customer request, we can also perform weld checks and non-destructive tests using penetrant liquids or radiographic testing, carried out in our factory and certified by EN/SNT level II qualified personnel. Thanks to our agreement with ACCREDIA accredited laboratories, we are able to perform laboratory tests and mechanical tests on request. The safety and quality of our end products are our top priority.
Surface finishing
For our most demanding customers, we are able to offer surface finish machining, with a choice among satin finishing, polishing or flower embossing on the inside or outside surface or on both sides. Once processing is completed, a check is carried out with calibrated (digital) roughness meters which automatically generate a report, guaranteeing maximum precision to full customer satisfaction.
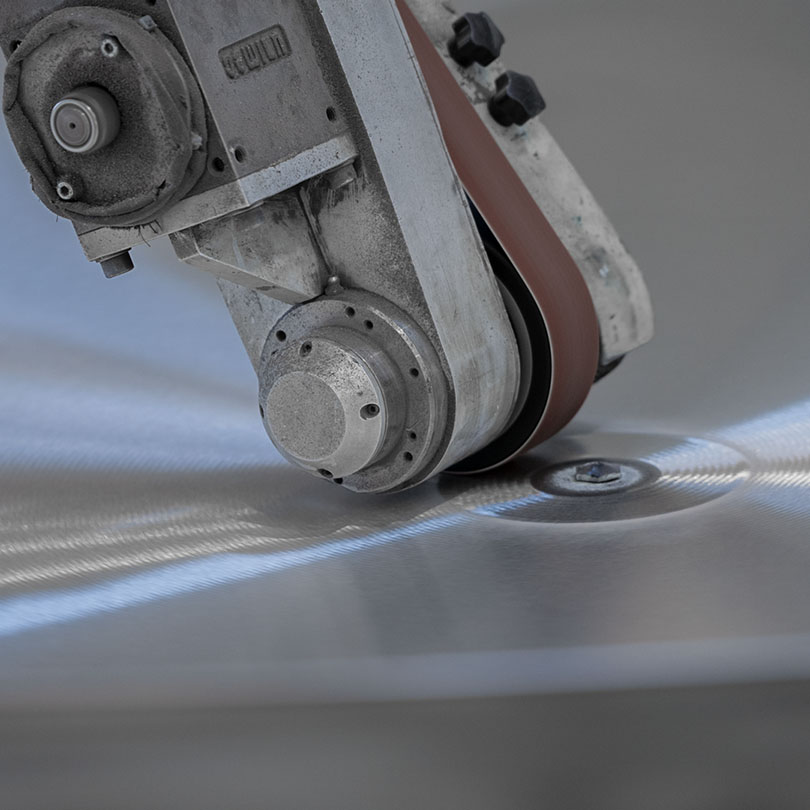
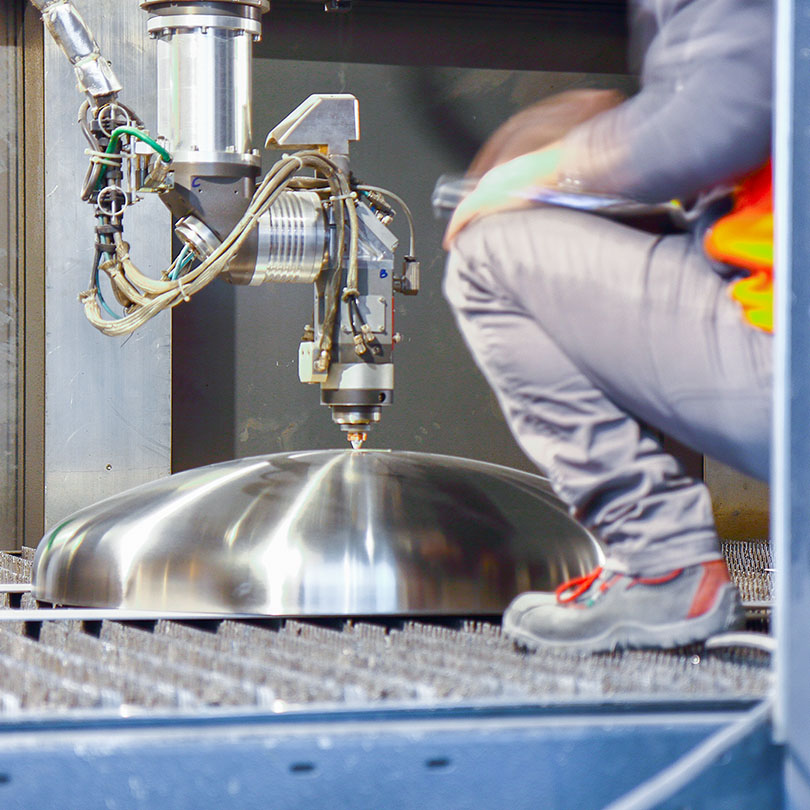
Drilling
Drilling to drawing is a highly customised process, which allows holes of different shapes and sizes to be obtained in the finished piece. Thanks to laser technology, we can also perform 3D drilling on the curved surface of a dished head, with millimetric precision. This will guarantee finished products perfectly suited to the specifications of the application for which they are intended. Thanks to the use of special dies, we are able to perform edged drilling with reworking options on the various types of head.
Bending
Sheet metal bending is a process allowing conical heads, conical reducers and ferrules to be obtained starting from metal plates. This technique involves hydraulic bending by means of rollers, with the metal plate caused to rotate between three or four cylindrical rollers with parallel axes until the ends meet, thus forming the desired product. Machining precision and quality are guaranteed by the use of a specific machine for sheet metal bending.
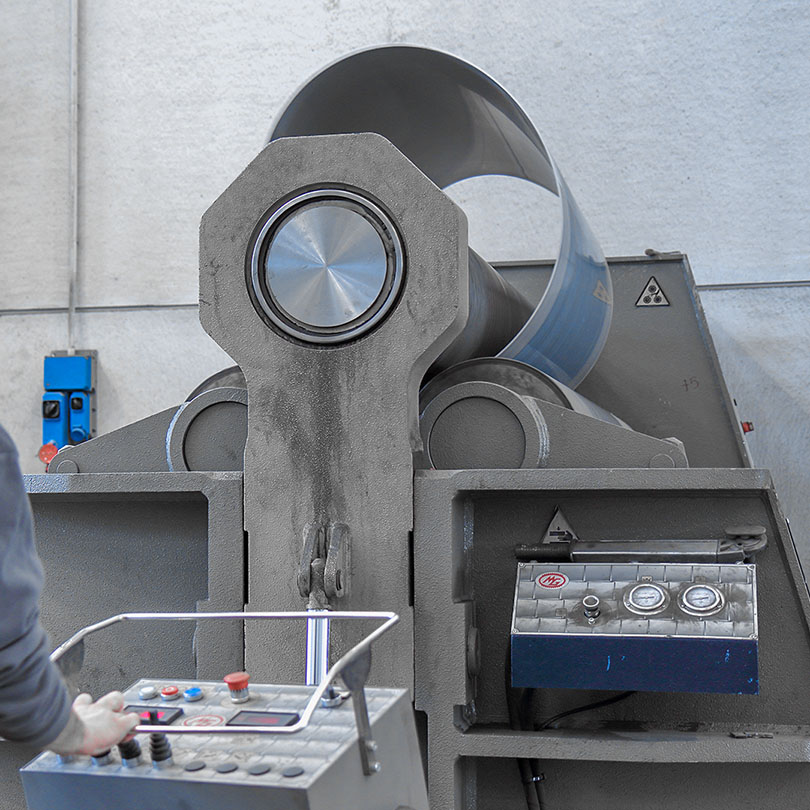
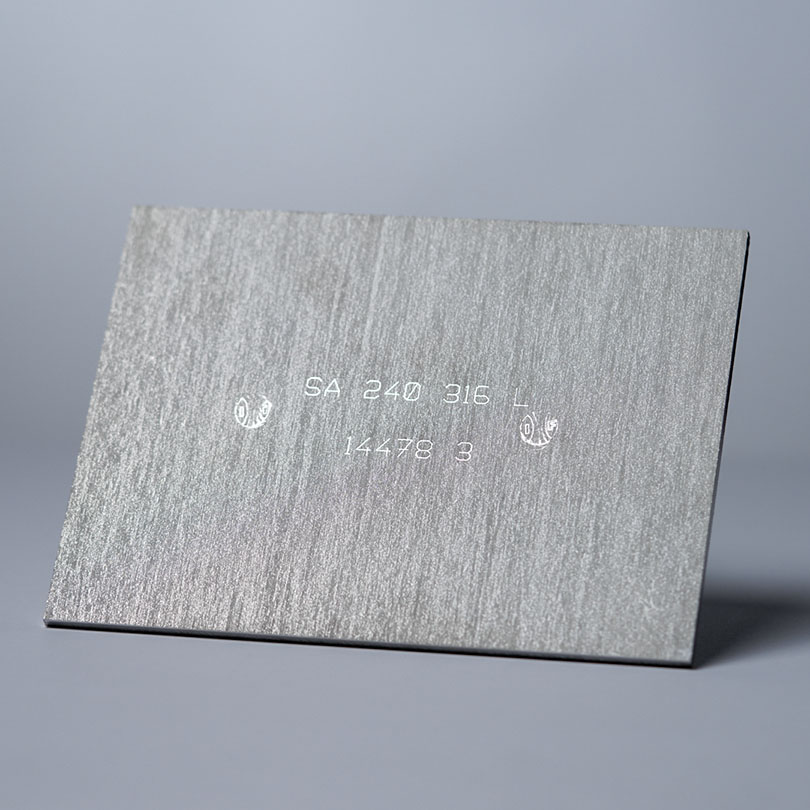
Marking
Marking of our stainless steel products can be done using different technologies. Laser marking guarantees precision and speed, without affecting the quality of stainless steel thanks to the low amount of heat released. Low stress marking uses a different technology that minimises the residual stress on the surface of stainless steel, protecting it from possible corrosion problems. Finally, chemical etching uses an acid to etch the metal surface, creating a permanent image. Each marking technology is chosen according to customer needs and product specifications.
International certifications
Alongside the Quality Certification granted by TÜV Italia, we also offer other certifications of technical conformity of our products.
In particular we are authorised to supply dished heads according to PED 2014/68/EU, ASME VIII Div.1, AD2000-MERKBLATT W 0, UKCA, TDT standards and to consequently release certificates for the construction of pressure vessels.
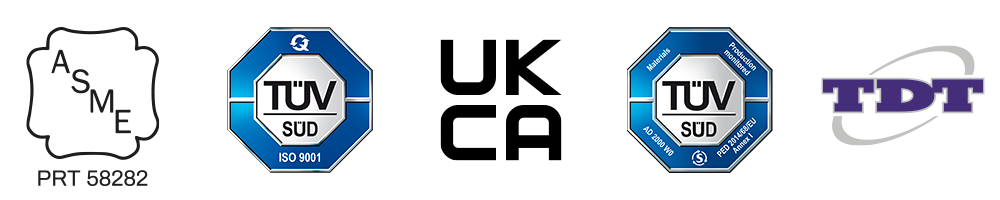